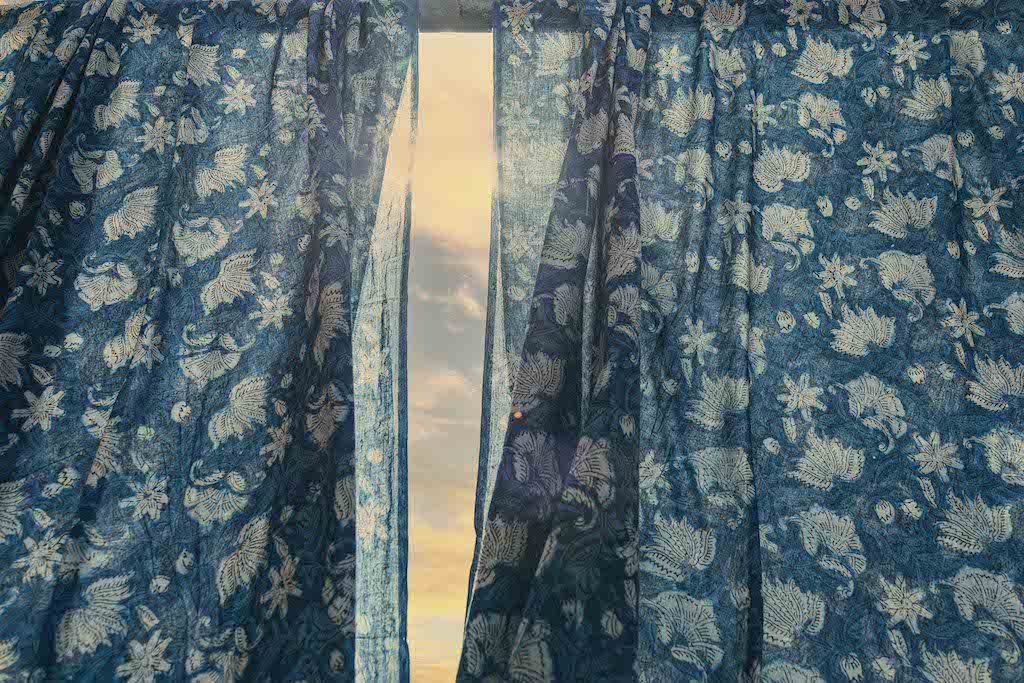

WE WELCOME YOU TO AN INSIGHT BEHIND OUR DRESSES...
For generations, this community has used hand-made teak blocks and plant extracts to print fabric - they maintained these indigenous practices even as the communities around them transitioned to chemical dyes.
Plants are where it's at...

IRISITABLE INIDGO
TYPICALLY, IN THE DYEING PROCESS, COTTON AND LINEN THREADS ARE USUALLY SOAKED AND DRIED 15-20 TIMES.
After dying, the yarn may be sun dried to deepen the colour. The process of Indigo dyeing is completely different while done using the traditional process, it’s 100% natural and often organic. Instead of using heat and a mordant, it is done using a living fermentation process that naturally sets the dye into the textile. The texture colouring process takes no less than seven days, from colouring till drying. At first the texture is dunked in a vat of dye and kept under the water for a couple of minutes. When brought out into the air, the shading is a splendid green and gradually it changes to a wonderful profound and rich blue of Indigo.
PRINTING WITH INDIGO
To create prints over and under the indigo dye is a whole other magical process... Dabu printing is a painstaking and a labour intensive process. The fabric is first received from the mills and washed to clear off surface impurities. The blocks are then dipped in natural dyes and meticulously hand printed on a plain fabric. The next step is to prepare mud resist mixture that's made with gum, lime and white chaff. This mixture is applied to the fabric and is then dried. Post drying, the fabric is dipped in a vat of dye, followed by a wash to remove excess dye and paste.
Once the fabric has been dyed and washed it's kissed by the sun and then washed some more...
As you can see this is a long and thoughtful process. One we are proud to be bringing you. From my last visit i was so touched and overwhelmed by the community sprit and involvement in this way of printing. It takes a village...quite literally!
We welcome our indigo collection next week! Join our mailing list for updates.
I really hope you can feel the love and sprit in each Indigo piece.
Huge thank you to Surbhi for our beautiful images and all my amazing team at Block Print Company